Blogging on a schedule seems to grow in difficulty over time. Issue No. 8 is here, which means I've been on the job for two months. That's still n00bville to most bloggers, but I've stopped holding my breath waiting to hit a stride or develop a sense of routine. If you've been reading
Work, you'll know that from issue to issue this magazine is anything but routine, and that might have something to do with it.
A far more likely cause is the fact that I'm now waist-deep in other projects. Springtime, for Tim, and TFWW, means priorities shift every minute. Getting anything done means enduring the sensation that I'm stealing time from other important tasks. I can't entertain any outside help for a good chunk of it, and perfunctory results are simply not an option. You can't phone in good design, and you can't phone in a decent blog. Even attempting to do so means that you think that the rest of the world won't see right through it. Arrogance.
Now what does all this have to do with
Work? With woodworking or shop practice? In a word: everything.
Who among us hasn't promised a loved one or a client some furniture object or something to be completed by a certain time? Chances are, if vivid memories of such a project are springing to mind, it was one you couldn't phone in either. Put another way, there were certain aspects of your endeavor not open to compromise.
It's OK. I mean I'm telling you it's OK. This is because, apart from diagnosable mania, a certain lack of compromise is often the thing that separates good work from great work. The trouble is, simply, that if you've got an unflinching timetable and an immutable design, the only thing left to rejigger is your working method.
Turn to page 115 in the current issue of
Work and put on your 3D glasses now.
"Some Lessons From An old Bureau" says it without saying it; the two most important words in constructive woodworking: cut list.
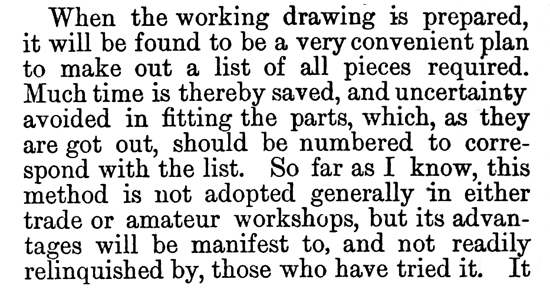
Until such time arrives that we may grow trees in the shape of the furniture we desire we're going to have to contend with wood projects that are made of assembled components, each one its own small wood project. It's all
delightfully recursive right up to the point where you overwhelm yourself. You need a cut list.
It's not just a piece of paper with tabulated scrawl, it's a mantra. Different professions use different incantations: punch list, shooting schedule, work breakdown structure, etc. In all cases, the higher concept is the same. Give yourself the benefit of a theoretical scaffold around the physical elements you intend to mess with, and you'll operate at a level of efficiency well worth the initial trouble.
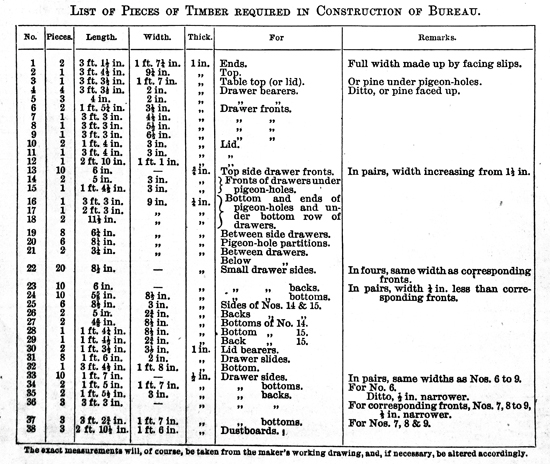
I realize this is old news to a lot of you, but it's a point that bears repeating for the benefit of the uninitiated. As recently as last week, I found myself consoling a friend who found himself smack dab in the middle of a large build project of his own devise, with no sense of how to complete it. He had a design and funding, but little else save for the rapidly approaching deadline. Funding meant the design couldn't change, but even if it could, what sense would it make to water down a design to suit poor working practices?
I told him, "If you have a design you can make a cut list. If you have a cut list you can build a materials manifest and a work schedule. When you have a work schedule you can put out a call for volunteers. All rivers flow from the mighty mountain. You will finish your project on time."
Shifting back to the issue at hand (literally), I'll say that the keenly important bits for me have a lot more to do with how to work, generally. As much as I'd like one, my schedule of projects doesn't have room for a carved coal scuttle. Thankfully, there's more to
Work than that.
By example, the gentle reminder in "Wrought Iron and Steel Girder Work" to have someone else look over my words and plans couldn't have been more timely.
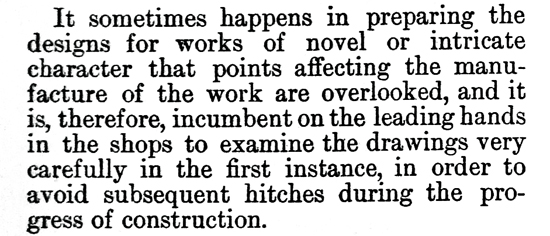
Before I get back to my drafting table, I'd like to thank Ben and Joel for all of the close examination they've given my ridiculous drawings, and I'd like to thank Halley for her tireless editing prowess, without which this blog would be woefully unreadable.
–TIM
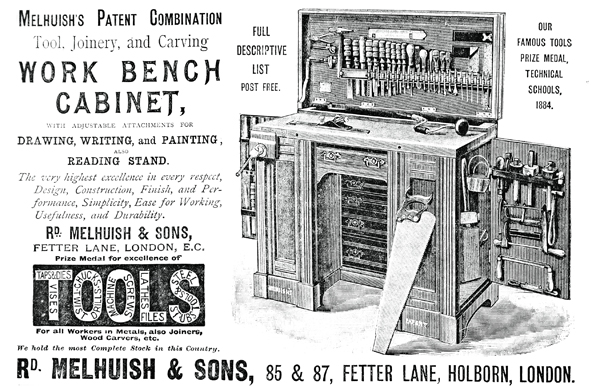
ARTICLES FOUND IN THIS ISSUE:
SOME LESSONS FROM AN OLD BUREAU • WROUGHT IRON AND STEEL GIRDER WORK
"TIPS" FOR TYROS • LATHES AND TURNING APPLIANCES
A COAL BOX IN CARVED OAK • HOW TO DRY NEGATIVES QUICKLY
NOTES FOR ELECTRO-PLATERS
OUR GUIDE TO GOOD THINGS • SHOP: A CORNER FOR THOSE WHO WANT TO TALK IT
• Click to Download Vol.1 - No. 8 •
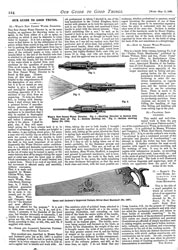
Disclaimer: Articles in Work: The Illustrated Weekly Journal for Mechanics describe materials and methods that would not be considered safe or advisable today. We are not responsible for the content of these magazines, and cannot take any responsibility for anyone attempting projects or procedures described therein.
The first issue of Work was published on March 23rd, 1889. The goal of this project is to release digital copies of the individual issues starting on the same date in 2012, effectively republishing the materials 123 years to the day from their original release.
The original printing was on thin, inexpensive paper. There are many cases of uneven inking and bleed-through from the page behind. Our copies of Work come from bound library volumes of these issues and are subject to unfavorable trimming, missing covers, etc. To minimize harm to these fragile volumes, we've undertaken the task of scanning the books ourselves. We do considerable post processing of the scans to make them clear but please bear with us if a margin is clipped too close, or a few words are unreadable. We would like to thank James Vasile and Karl Fogel for their help in supplying us with a book scanner and generally enabling this project to get off the ground.
You are welcome to download, print, and pretty much do what you want with the scan for your own personal purposes. Feel free to post a link or a copy on your blog or website. All we ask is a link back to the original project and this blog. We are not answering requests for commercial downloads or reprinting at this time.
2) click on the save icon in the PDF view to save the issue.
or
directly from the blog entry right click on the download image and then select "save link as" to save the pdf to your computer.